Microstructure and Mechanical Properties Characterization of Directed Energy Deposited AlCuFeNiTi High Entropy Alloy
An equiatomic AlCuFeNiTi high entropy alloy (HEA) was successfully fabricated for the first time using pre-alloyed powder with the directed energy deposition method on a Ti6Al4V substrate. The alloy was characterized using scanning electron microscopy (SEM), electron backscatter diffraction (EBSD), X-ray diffraction (XRD), and nanoindentation to provide insight into the relationship between its microstructural and nanoscale mechanical properties. Energy dispersive x-ray spectroscopy (EDS) results reveal three distinct regions, a consequence of variation in local elemental composition within the alloy that also influences its mechanical properties. The alloy was found to be multiphase with mostly ordered BCC structure (B2) and a small amount of FCC structure with traces of C14 Laves. During the solidification process, evidence of dendritic fragmentation was observed, which contributed to the alloy having mostly equiaxed grains rather than the commonly observed columnar grains in previously reported additively manufactured high entropy alloys. Nanoindentation results showed that the dendrites constitute a hard zone, whereas the inter-dendritic regions typify a continuous soft zone with dispersed Laves precipitates, strengthening the grain boundaries. The results of the current study highlight the synthesis of an equiaxed HEA with one of the highest combinations of elastic modulus and hardness values determined using nanoindentation.
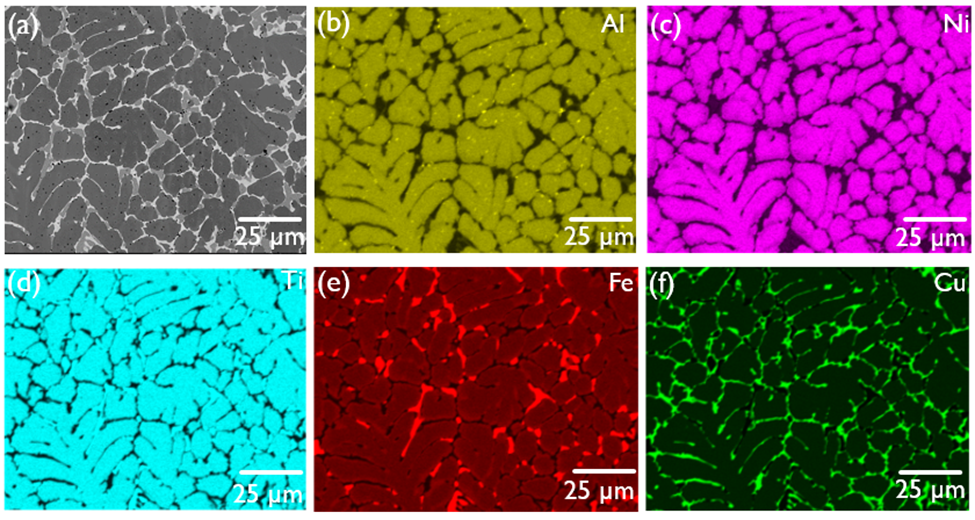
Comparative Investigation of AlCoCrFeNi High-Entropy Alloy Manufactured via Directed Energy Deposition and Binder Jetting Additive Manufacturing Routes: Characterization, Microstructural Analysis, and Isothermal Treatments
Additively manufactured high-entropy alloys are in a critical stage of development. More studies are required on how their compositions, processing routes, and microstructural evolutions intertwine to influence their (mechanical) properties for various fields of applications. In this study, equiatomic AlCoCrFeNi high-entropy alloys were fabricated via two additive manufacturing routes: binder jetting 3-D printing (BJ3DP) and directed energy deposition (DED). The response of the samples to isothermal heat treatment was investigated and compared with the as-printed samples. Their microstructural evolutions were studied with scanning electron microscopy (SEM), energy dispersive spectroscopy (EDS), X-ray diffractometer (XRD), and backscattered electron diffraction (EBSD). Nanoindentation was used to characterize their mechanical properties. The results show that the binder jetting and DED samples respond differently to isothermal heat treatments, as diffusion mechanisms like grain boundary precipitation, precipitate-free zones (PFZs), and Widmanstatten structures are more observable in the binder jetting samples. Furthermore, the binder jetting samples exhibit higher values of mechanical properties than the DED samples. The study provides significant insights into the differences in microstructural morphology, diffusion phenomena, and evolution of the alloy manufactured via the two additive manufacturing (AM) routes. The insights gained from this study may help to improve the fabrication and properties of AlCoCrFeNi HEA via the two additive manufacturing routes for applications in tooling, automobile, structures, and aerospace industries.
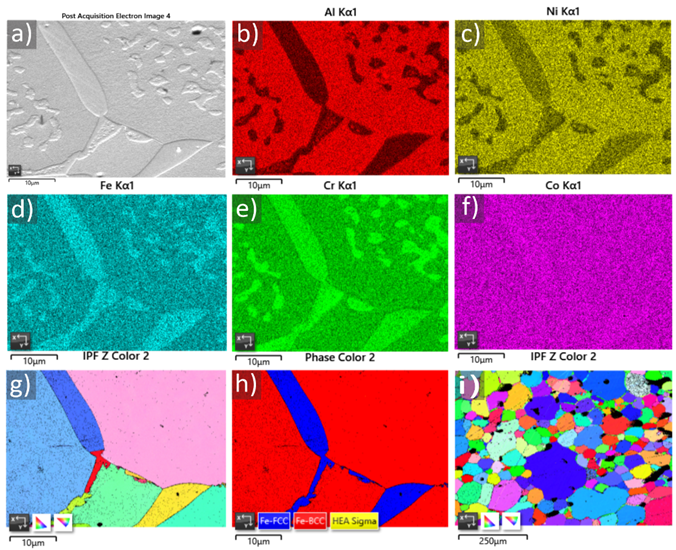